fatigue testing machine calculation|rotating fatigue machine : manufacture Luckily, the process of performing proper fatigue calculations can be at least partially automated allowing for ease of use and reducing calculation errors. In a short series of articles starting with this one, I will cover the basics of fatigue analysis in several categories. web9 de dez. de 2023 · A Caixa Econômica Federal (CEF) realizou o sorteio do concurso 102 da +Milionária neste sábado (9). Confira os resultados a seguir: Dezenas sorteadas: 41-15 .
{plog:ftitle_list}
1 dia atrás · Today we’re announcing the public preview of Microsoft Copilot for Finance, the newest Copilot offering designed for business functions that extends Microsoft Copilot for .
Luckily, the process of performing proper fatigue calculations can be at least partially automated allowing for ease of use and reducing calculation errors. In a short series of articles starting with this one, I will cover the basics of fatigue analysis in several categories.
From understanding the fundamental purpose and types of fatigue testing, including Mechanical Fatigue, Creep Fatigue, Thermo-mechanical Fatigue, Corrosion Fatigue, and Fretting Fatigue, we’ve examined the intricate details .The eFatigue website gives you easy access to modern fatigue analysis tools and technology from any web browser— everything you need for computing the fatigue lives of metallic .The MTS TestSuite ADVLCF module includes the activities, calculations, and test and report templates you need to run constant-amplitude strain-controlled fatigue testing up to 12 Hz, .
Instron manufactures tensile, compression, fatigue, impact, rheology, and structural testing machines, testing a variety of materials and range of applications. Telephone: +1 800 877 6674fatigue testing machine using pneumatic cylinder and microcontroller. With the help of this machine, we can . values, control the output pins, and perform any calculations or logic neededfor the testing process. Within the loop function, you will need to . In this project, stress life approach is adopted. It is the first method used for fatigue calculation. This approach is simple based on S-N curve also known . Then, the specimens were loaded on the rotating bending fatigue test machine, and test was carried out according to Japan Society of Mechanical Engineers (1981) test method. .Key Terms. Fatigue: Fatigue failure is a time dependent failure of a material or component due to a cyclic stress that is lower than the material’s Elastic Limit or Ultimate Tensile Strength. Fatigue is generally associated with tensile stresses but there are special circumstances when it can occur in compression. Frequency: Frequency is a measure of the number of tension and .
High Cycle vs. Low Cycle Fatigue. It is already explained that for describing the fatigue strength, apart from the stress value the number of cycles is also require. If this number of cycle is unto 10^3 then the fatigue situation is called as low cycle fatigue. If the number of cycle is more than 10^3 to 10^6 then it is called high cycle fatigue.Fatigue design curves are generated from test data by applying large safety margins to the average property curve. While considering material fatigue in design, an additional safety margin is often applied against the cycles-to-failure at a given stress amplitude. . Calculation of the fatigue stresses: Caesar II automatically does this . Fatigue testing machine is a kind of equipment commonly used in the field of machinery manufacturing, the application of high-end equipment materials research and structural design is particularly important, its technical parameters include static force, dynamic force, strain, coaxially, etc., the accurate calibration is a guarantee of the reliability and .
governing the design of the fatigue machine is based on elastic beam bending principle[4] .Experimental values of fatigue life are verified using theoretical calculations. 1.1 DESIGN OBJECTIVES This aims at designing and constructing a rotating bending fatigue testing machine that is capable of testing the fatigue life of various samples of .to Fatigue Testing of Metals E466 Conducting Force Controlled Constant Amplitude Axial Fatigue Tests of Metallic Materials. E467 Verification of Constant Amplitude Dynamic Forces in an Axial Fatigue Testing System. E468 Presentation of Constant Amplitude Fatigue Test Results for Metallic Materials. E606 Strain-Controlled Fatigue Testing. The developed fatigue strength testing machine had a designed machine capacity of 18875Nmm that sustained a motor power of 5.93kw.The machine shaft diameter determined to be 9.88mm developed an . The experimental fatigue life and load rate are determined on a full scale leaf spring testing machine. Four alternate methods of fatigue life assessment have been depicted. Firstly by SAE spring design manual approach the fatigue test stroke is established and by the intersection of maximum and initial stress the fatigue life is predicted.
The MTS TestSuite LCF module contains the test and report templates and calculations you need for low-cycle fatigue (LCF) testing up to 12 Hz in strain control, using an extensometer as a feedback transducer. Predefined test templates let you efficiently test to ASTM E606 and D3479 strain-controlled low-cycle fatigue test standards. Plus, you .
As it is known, there are a great many factors to be considered during the study of fatigue phenomena. The methods of fatigue failure analysis are inexact and only approximate results can be obtained. Thus, more-exact methods require that more data be derived from practical testing and statistical calculation. Test setup. The fatigue test not only exposes standardized specimens but also entire components to vibrational loading. For this purpose, the sample is clamped in a device similar to a tensile testing machine. While the lower clamping device is statically connected to the environment, the upper clamping device is dynamically vibrated by resonance.Shop Fatigue Test Machines. How Does a Fatigue Testing Machine Work? Fatigue test machines are built to evaluate the strength of raw materials, components or finished products. Fatigue testing machines measure the .
types of fatigue testing machine
The EJMA calculations for this test was based on compressing the bellows 2.3/4” 1000 times. This bellows was attached to each side of the cylinder of the fatigue test machine and pressurized to 25 PSIG for the purpose of leak .Electromechanical Fatigue Testing Systems. The eXpert 5900 series tabletop dynamic testing machine is a compact, quiet, and clean electrodynamic testing system for determining the durability of materials and components in tension, .
Fatigue testing machines usually apply cyclic loads to test specimens. Therefore, fatigue testing is a dynamic testing mode, which can be used to simulate . methods for measurement and calculation of fatigue life as . 2019 Nr 1(10) s. 80-108 WOJCIECH MACEK, STANISŁAW ZAWIŚLAK, ADAM DEPTUŁA,
the machine. 2. Fatigue Test: The lab TA will conduct a constant amplitude, tension-tension fatigue test on a dogbone sample up to fracture. Measure the sample prior to testing and record its’ dimensions; document the testing parameters used (waveform, maximum & minimum load, frequency, etc.). 3.- The results of a fatigue test using a nonzero mean stress are . plotted on a Haigh diagram with lines of constant life drawn . through the data points. . Calculate S. n. by using Goodman relationship (4) The value for S. n. can now be entered on the S-N. diagram to determine the life of the component, N. f.Introduction to fatigue An early example of testing to determine the fatigue strength of a component was reported by W.A.J. Albert in 1838. He investigated the fatigue failure of chains used to haul trucks in mine shafts (Ref 1.1). Examples of the chains were tested using a purpose-built test rig (Figure 1.2). The weight was raised and
An electro-hydraulic fatigue testing machine was used for both static tensile-shear tests and fatigue tests. Fatigue experiments were performed using a sinusoidal waveform under a load control with a frequency of 10Hz and a stress ratio of R .Empirical approaches based (e.g., Coffin-Manson equation [193]) or theoretical models based (e.g., Murakami model [194]) numerical calculation provides available means to estimate the fatigue life of defect-included AMed parts, enabling further quantification of the sensitivity of fatigue resistance to porosity [195–197]. Table 2 summarizes several common fatigue life .In order to reach the optimal set of working parameters, manufacturers will evaluate the springs with a universal testing machine to see if any of these factors have altered the final product. Universal testing systems can help characterize these properties, including the spring constant, free height, and solid height.
We use for the calculations the values provided by the test machine. By setting different ratios between τ and σ, several points can be obtained within the variation curve between the shear stress and the normal stress. . Ogawa F, Shimizu Y, Bressan S, Morishita T, Itoh T (2019) Bending and torsion fatigue-testing machine developed for . Background Traditional fatigue testing methods can be expensive due to the need of specialised equipment for engineering materials and structures. Thus, a new fatigue testing approach utilising machining cutting forces to induce cyclic stresses, enabling fatigue life assessment of engineering materials and structures, has been developed. Objective This . Fatigue machine is also known as fatigue test machine, fatigue strength tester, or fatigue tester. 3 Most Common Uses of a Fatigue Testing Machine: Fatigue tests are critical in manufacturing because they determine a material’s lifespan. One can conduct fatigue tests in a laboratory setting.
rotating fatigue testing machine
tensile strength 2x4
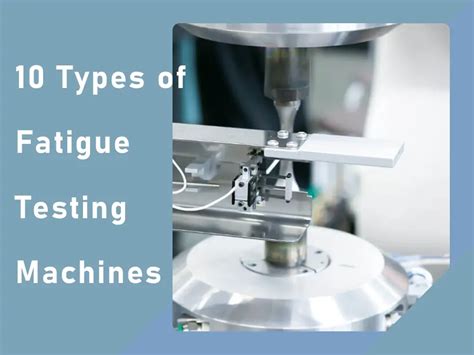
tensile test chart
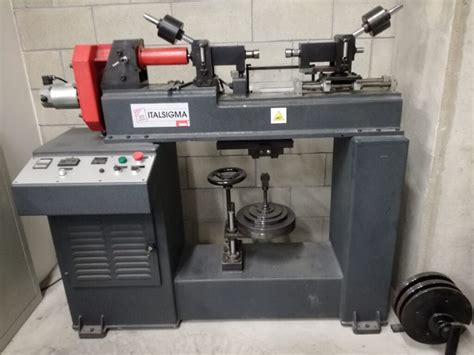
rotating fatigue machine
10. 11. 12. Next. 360p. Coroa safadinha. 2 min Carlos5043675 - 360p. milf - coroa vadia da bunda grande fodendo blog amador com. 4 min Drummerpower - 360p. novinha da .
fatigue testing machine calculation|rotating fatigue machine